Food manufacturing company reduces reactive maintenance up to 60%
When a new manager took over the maintenance department of a food manufacturing company, he knew the company needed to move toward a more proactive system, so he tried out UpKeep.
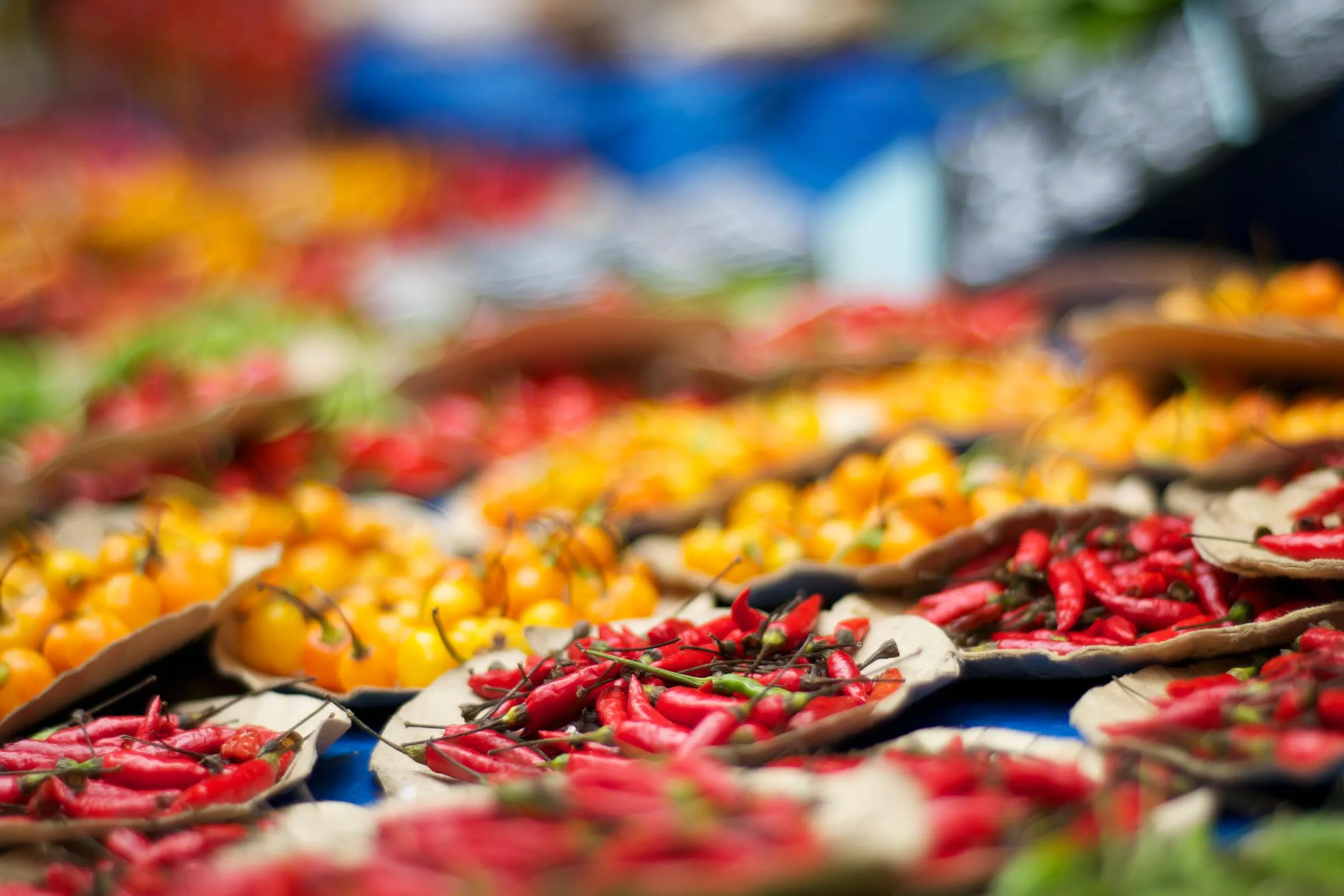
Challenge
The maintenance team at this manufacturing company was nearly always in reactive maintenance mode. Requests were handled through phone calls and emails, while no information was recorded. In addition, much of the plant’s equipment was custom-built or retrofitted, which meant that replacement parts were difficult to obtain. When machinery went down, production lines were affected for weeks.
Solution
Although the company had purchased another software solution, it proved too complex for the staff to use. The manager learned about UpKeep’s Asset Operations Management solution from a sister site. After the first month, email communications dropped by 90 percent. Requesters are now entering good information, and the company’s accountability and traceability have improved significantly.
Results
Since the organization operates many custom-built machines, staying on top of ordering replacement parts can go a long way in reducing downtime. This can result in significant savings. For example, getting one particular machine up and running one day sooner saves this company $40,000.
In addition, the business recoups labor costs when machines can be repaired in a timely manner. This organization reports that one production line going down for two hours will cost it $18,000 if employees have nothing to do. Not only can this be reduced or eliminated through a more efficient maintenance system, but this labor can be redirected to preventive maintenance tasks more effectively during downtimes.
Also, email messages have been reduced by 90 percent because everyone is entering information directly into the system.
As far as KPIs, the company is working to reduce reactive maintenance as a percentage of its preventive maintenance program. The team has gone from not tracking anything to tracking work orders and wrench time and they have seen a reduction in reactive maintenance from 100 percent to no more than 60 percent.
Specialized equipment downtime can cost upwards of $2.4 million in losses
The company operates many pieces of machinery that are either custom-built or retrofitted from another use. As a result, it can be difficult to quickly source machinery replacement parts. Sometimes, the parts that need to be custom-made can take up to three months to replace, which impacts the entire company's bottom line.
For example, a packaging machine failure severely impacted the business before using UpKeep. For six days per week and 18 hours per day, the team relied on a production machine that was custom-built. Now, the machine is past its warranty date and is beginning to break, due to heavy use and a lack of regular inspections. In response, the maintenance team retrofitted an older machine as a backup. However, the backup machine is much slower. The original machine can run 64,000 items per day. When it breaks and the company is waiting for parts for up to 12 weeks, the slower machine can only handle 54,000 per day. Each item resells at $4 each, so the company loses $40,000 per day while the main machine is down.
In other words, if the custom-built machine is down for 60 business days (12 weeks), the company would lose upwards of $2.4 million worth of products, just from waiting on the proper parts to arrive.
UpKeep prevents asset downtime by notifying when parts need replacement
UpKeep helps the company to better anticipate replacement part needs and prevent time-lags in the production line. By scrolling through the parts tab on his phone, a manager can see exactly the status of all parts. Parts can be ordered before the machine requires them to reduce overall downtime. By using UpKeep, maintenance technicians know the whereabouts and needs of all machinery parts, preventing significant production losses. UpKeep provides the tools to implement a preventive maintenance program, improving overall equipment effectiveness and reliability.
Easier audits with UpKeep
Although the manufacturer knew it needed to change the way it was handling maintenance work, one of the key drivers was the required yearly audit.
Every 12 months, the audit team needed schedules, work order history, and other similar items.. Before UpKeep, the team did not have this documentation, which made it difficult to report when audits came around.
Now, the team can scroll through the work order history tab in UpKeep. They love the increased traceability of every job and accountability of assigned work orders. Audits are made easy with a system in place that keeps tabs on all previous machinery inspections and fixes.
Clear historic data using UpKeep
Since important information was not written down or recorded before UpKeep, the responsibility was on team members to remember all plant knowledge and work order history. A lack of written records resulted in confusion, causing many unnecessary phone calls and questions, as well as inconsistent and incomplete knowledge transference between teams.
Now they can see all work order history with UpKeep.
Technicians no longer rely on word-of-mouth communication to implement fixes. Now, they simply scroll through UpKeep on an iPad and know exactly the status of work orders and what needs to be done for the day.
Company saves over $18,000 with increased labor productivity
In addition, lost labor productivity is significant when a line goes down. For example, if one line goes down for two hours, that costs the company $18,000 just in terms of people standing around with nothing to do.
Now, technicians are busy with preventive maintenance checks on all equipment and parts. Every morning, technicians open UpKeep on one of the plant's iPads and perform routine inspections on machines they never used to check regularly. By following a preventive maintenance checklist on UpKeep, technicians have become better at their jobs. For example, while performing a preventive maintenance check on equipment, a technician noticed that some of these machines loosened their screws and needed adjustments. Had the technician not done a preventive maintenance check, this small detail could have affected everything in the plant. Now, routine checks are performed on these screws, to ensure continuous smooth operation.
Streamlined efficiency and improved communication
Although the company is still in the early stages of implementation, the time savings are already apparent.
Email has gone down by 90 percent because everyone is entering information directly into the system. The maintenance manager used to be busy all day, putting in overtime, and not getting everything done. Now he can stay busy for 8 hours but get the required work done plus some extra projects. He can also access the system from home to assign work orders on the night shift.
In the past, he spent time walking around to see what people wanted to fix in order to approve or decline requests. Now, he can simply look at photos uploaded onto UpKeep's work orders and make that determination, accessing UpKeep from anywhere and seeing information instantly.
Smooth implementation
Rollout and implementation were smooth. After spending a few weeks setting up the system, the team said it took about a month to get everyone used to using UpKeep. Requesters, which include shift leaders and technical staff, are now entering complete, quality data in the work requests. Many others in the company have view-only access, so they can check progress on their own time.
Reduced reactive maintenance up to 60%
As far as KPIs, the company is working to reduce reactive maintenance as a percentage of its preventive maintenance program.
The team wasn’t tracking anything before and now, they are tracking how many work orders come in and how much wrench time is spent on them. The first goal is to reduce reactive maintenance to no more than 60 percent, which has already been accomplished a few times.
Want to keep reading?
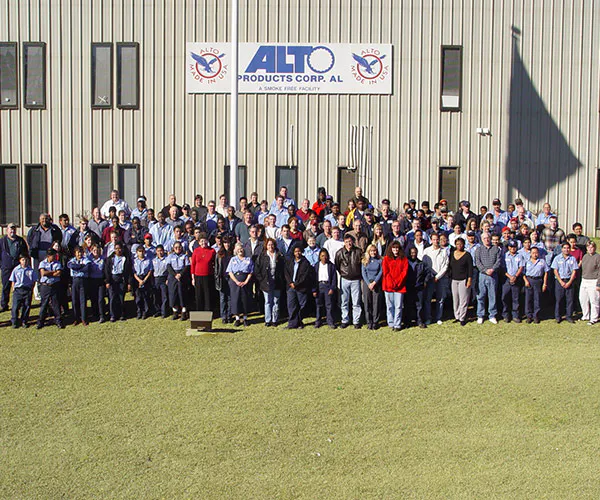
Equipment / Manufacturing
Alto Products moves from reactive to preventive maintenance
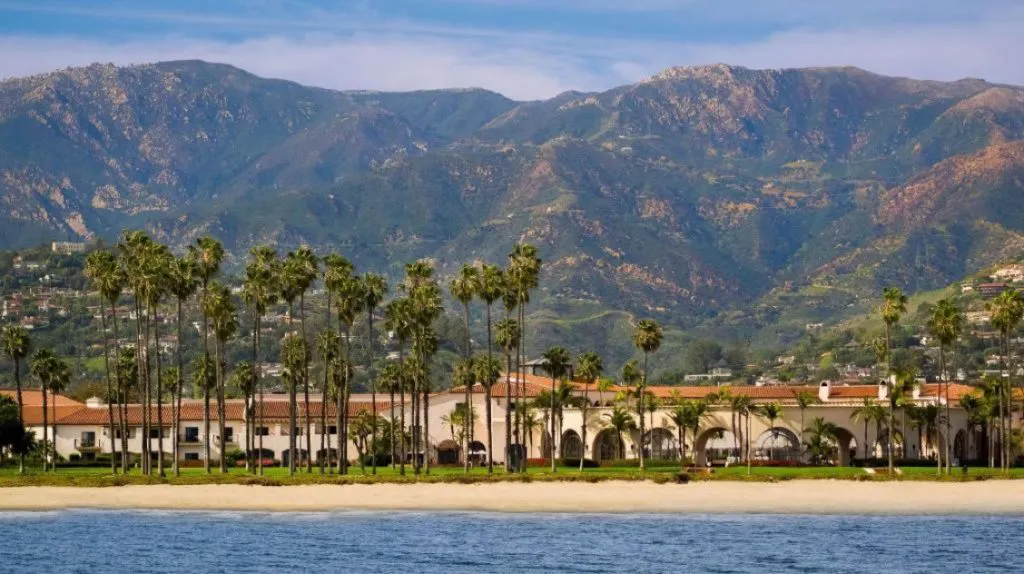
Equipment / Manufacturing
Innovative Micro Technology creates a safety-focused culture
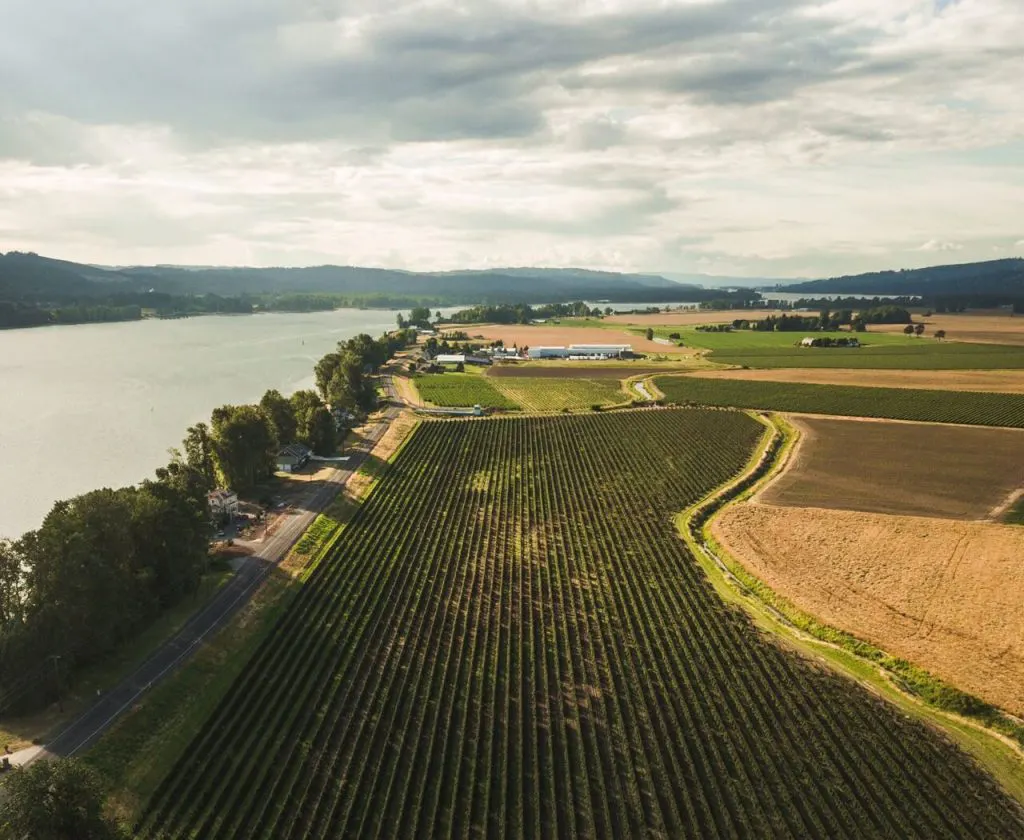
Equipment / Manufacturing
Columbia Fruit saves money with organized inventory
4,000+ COMPANIES RELY ON ASSET OPERATIONS MANAGEMENT
Leading the Way to a Better Future for Maintenance and Reliability
Your asset and equipment data doesn't belong in a silo. UpKeep makes it simple to see where everything stands, all in one place. That means less guesswork and more time to focus on what matters.
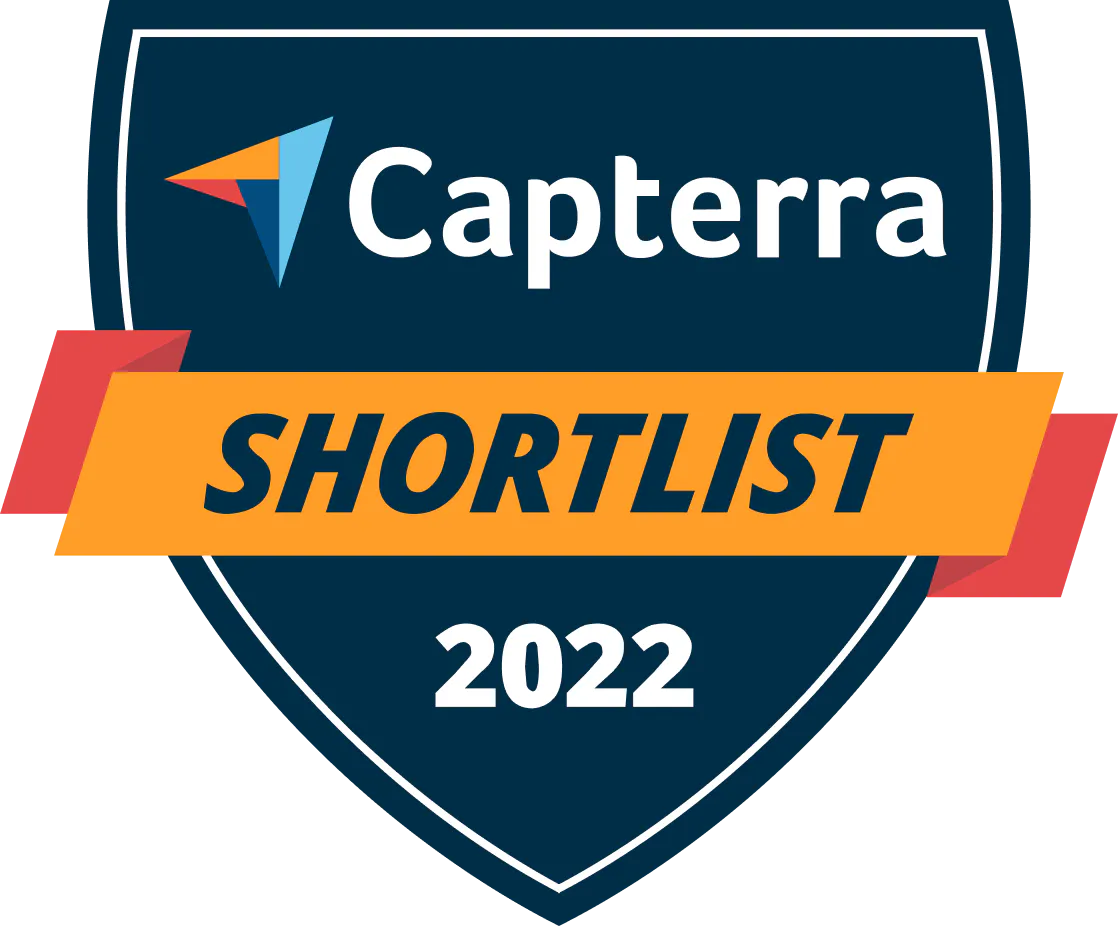

![[Review Badge] GetApp CMMS 2022 (Dark)](https://www.datocms-assets.com/38028/1673900459-get-app-logo-dark.png?auto=compress&fm=webp&w=347)
![[Review Badge] Gartner Peer Insights (Dark)](https://www.datocms-assets.com/38028/1673900494-gartner-logo-dark.png?auto=compress&fm=webp&w=336)
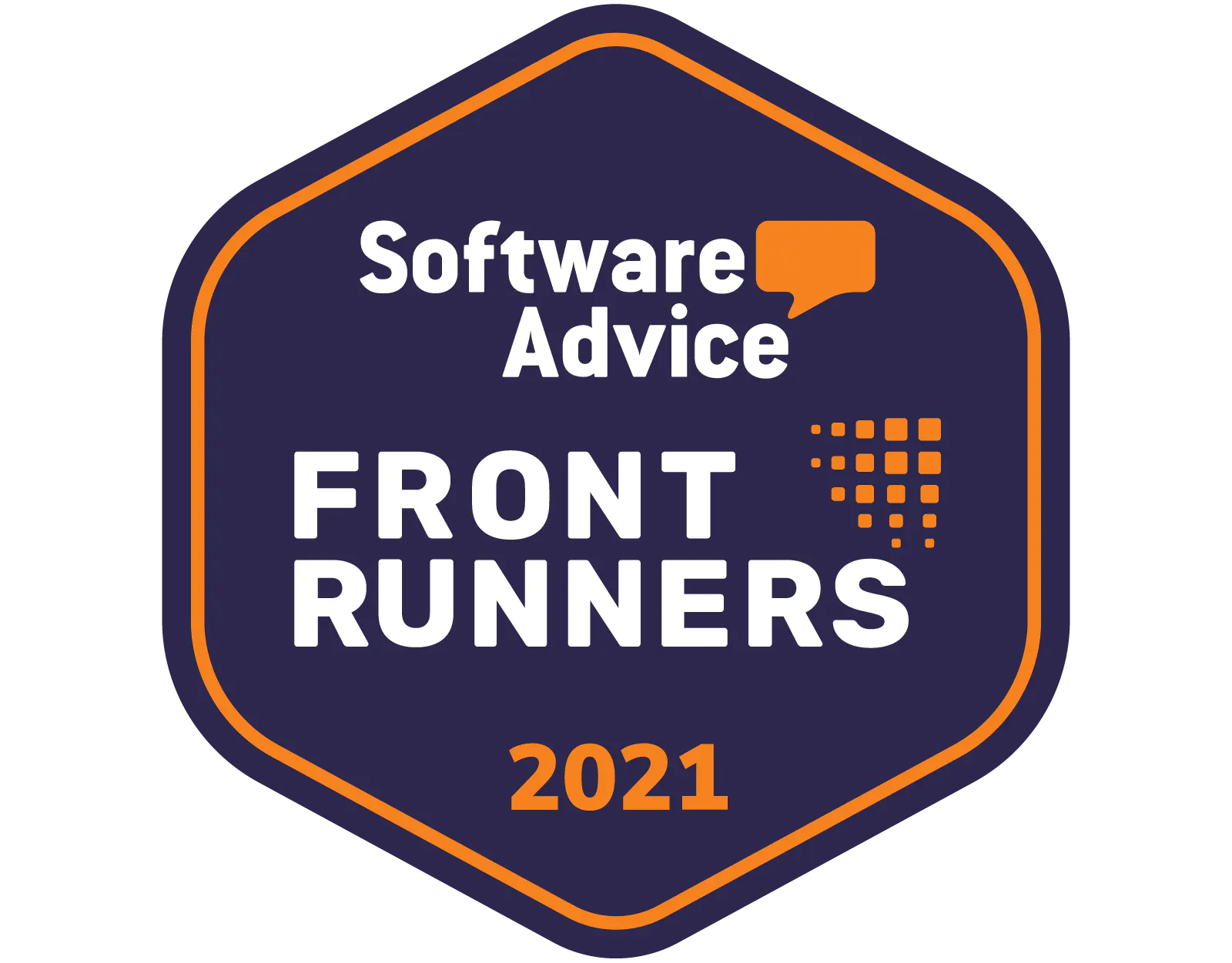